Making the First Hundred Better Body Bag Prototypes: Production
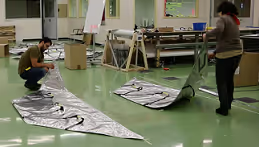
Our previous blogpost detailed the organisation phase required prior to the manufacturing the first hundred prototypes of the Better Body Bag. This blogpost will detail the production aspect of building a prototype, including the brainstorm-based action reigning throughout the process.
First of all, before going any further into the post, it is important to mention that the prototype manufacturing period was a great time to be alive. Not only is the Better Body Bag project innovative, but the procedure to get to the final product was innovative as well. To have the opportunity to work in such a diverse team, that allows you to explore non-conventional solutions to longstanding issues, can only be positive for the project as it exposes itself to multiple angles. Not to mention self-development as well.
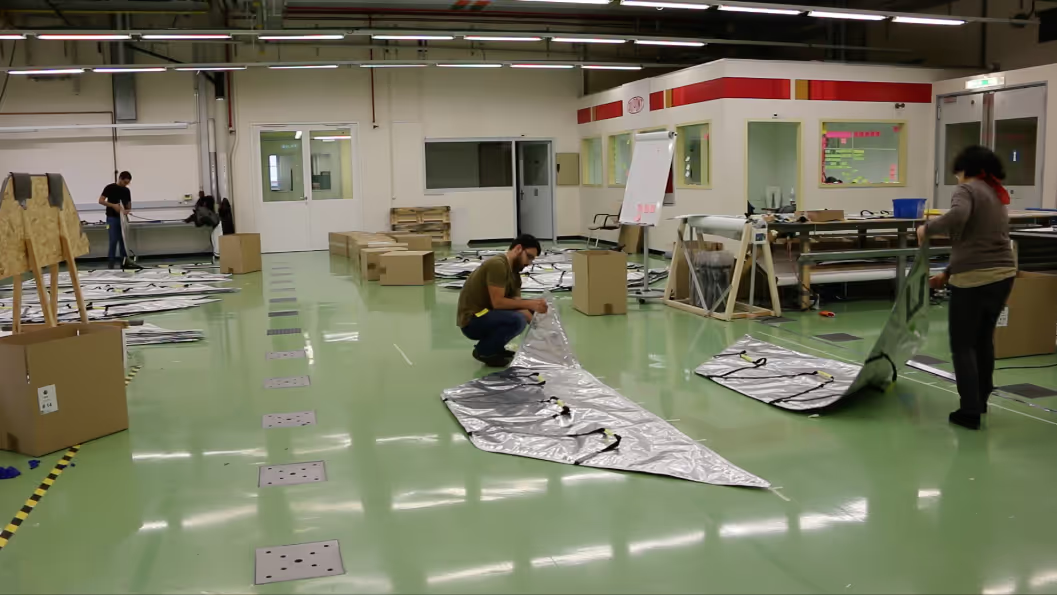
The notion of a prototype being a preliminary version of an item that can still be developed provided a freedom to explore variations to develop the best design possible. The variations were not only based on features, but also finding the most optimal manner to manufacture the Better Body Bags. Suggestions came mainly from our team members and volunteers, but also from individuals from Geneva Humanitarian Lab, DuPont and the International Committee of the Red Cross (ICRC) that passed through during the many presentations we did in the "manufacturing”period.
To ensure that feedback was received correctly on the different variants - each bag was numbered and tracked on an excel sheet – the first part of the quantitative survey, that Social Solutions Research Association provided with the Better Body Bags, included the numbers of the bags being tested.
A typical daily morning routine during the manufacturing process would include the following:
- 8:30 am - Arrive at DuPont
- 8:35 am – Have a coffee with the rest of the team and discuss where we currently are in regards to our estimated agenda
- 8:55 am – Distribute the tasks and update agendas and estimation of time until the end of production.
- 9:00 am – “Get to work!” (said by no one in particular, just a collective thought)
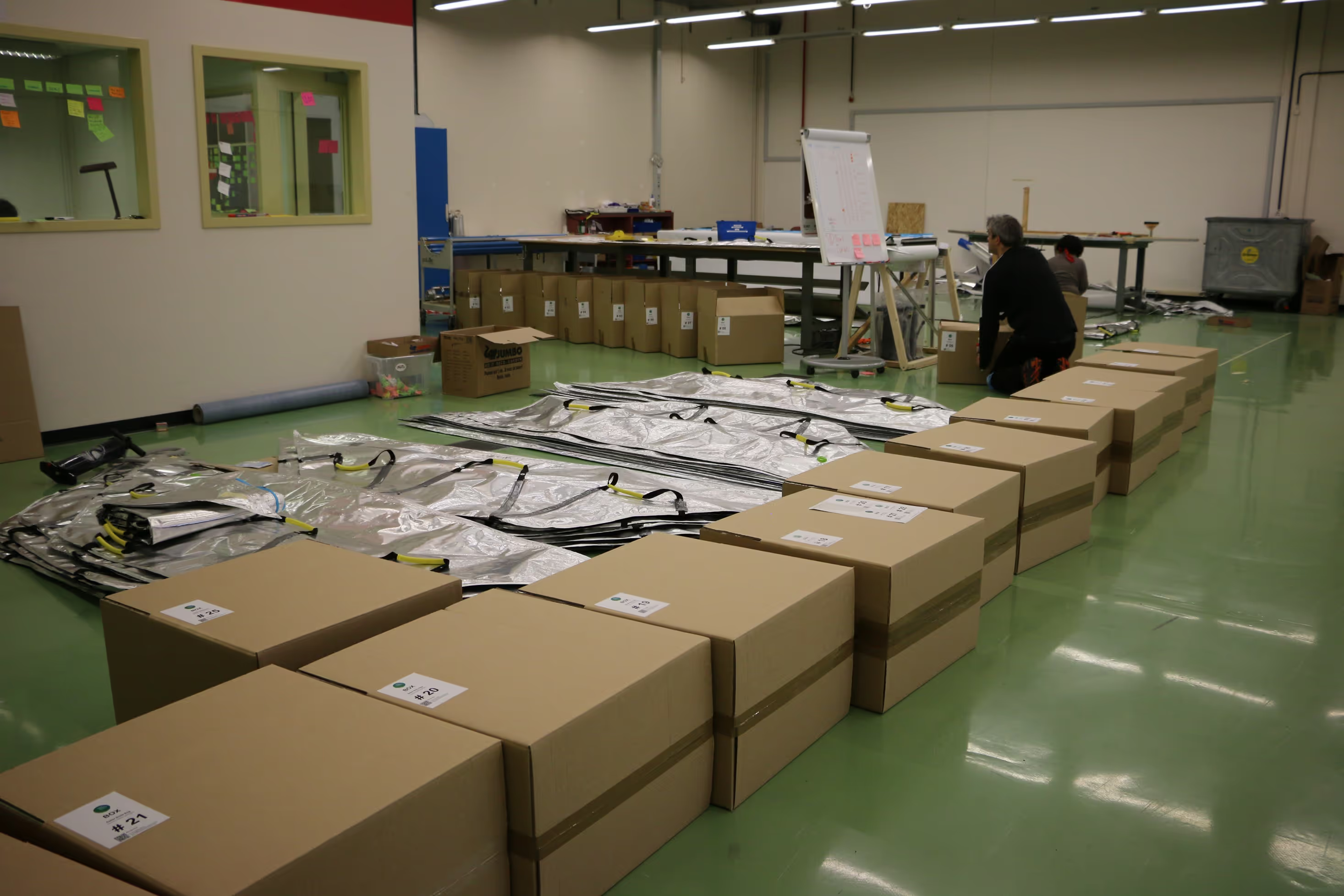
In terms of task distribution, we attempted to diversify it as much as possible so that no one would get stuck with repetitive work. However, Joao very quickly became the most qualified Zipper crimper and, sadly for him, was so good at it that it became his predominant task. To avoid having to do all this individual work in collective silence, we very quickly introduced music to the process. If you keep in mind that those who were present the most during this period, worked more or less 160 hours – you’ll realise that that there is A LOT of time to explore your past and current musical tastes. Music ranged from Fela Kuti to the Backstreet Boys passing by Missy Elliott and finishing with Portuguese Children’s Television music! Not only did we get to develop our crimping skills but also got to broaden our musical knowledge – could it get any better?
The bags were manufactured in a space kindly provided by DuPont where each individual working on the production process had to go through a brief safety and security training (+1 for being responsible and protected!). The building phase involved more than 14 people with diverse professional backgrounds and different incentives to participate in this project - any reason is always a good reason to help out!
Then finally came the day when Annuka handed in the completion of one month's work to the warehouse of the ICRC. The bags were divided into boxes with two different types of content: one type had five Better Body Bags per box and the other had four Better Body Bags and a pump for the vacuum feature of the bag.
Stay updated
Sign up for our newsletter to receive regular updates on resources, news, and insights like this. Don’t miss out on important information that can help you stay informed and engaged.
Related articles
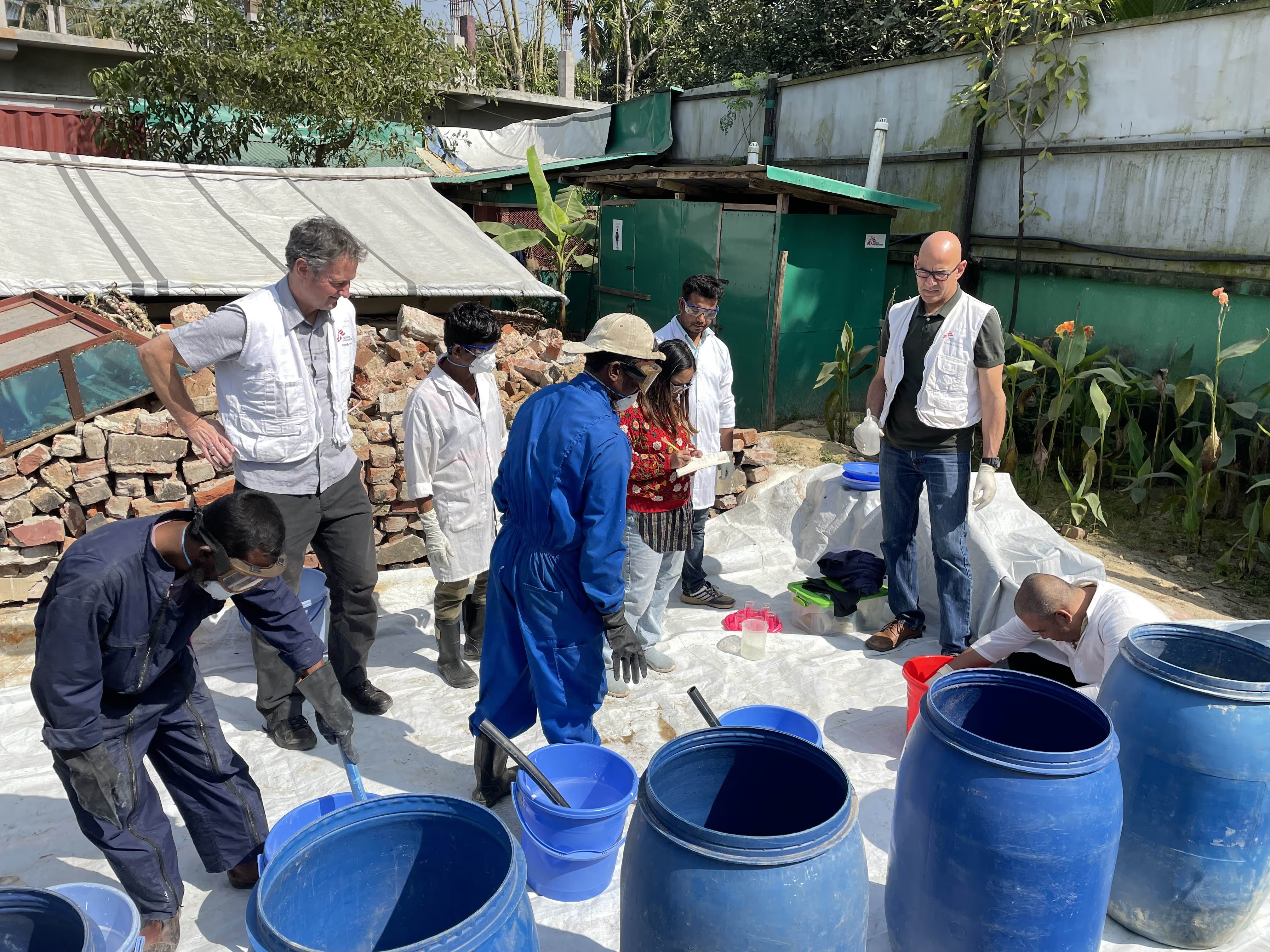
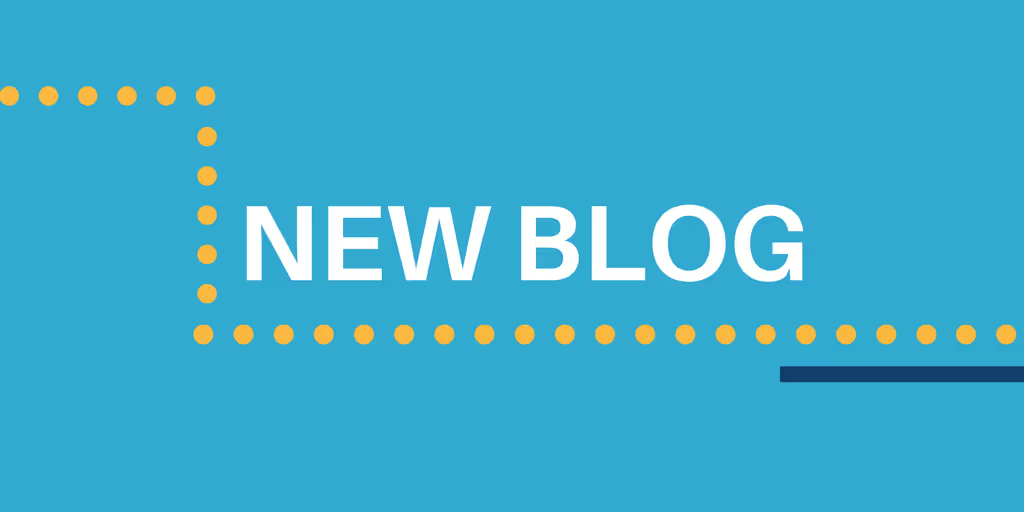
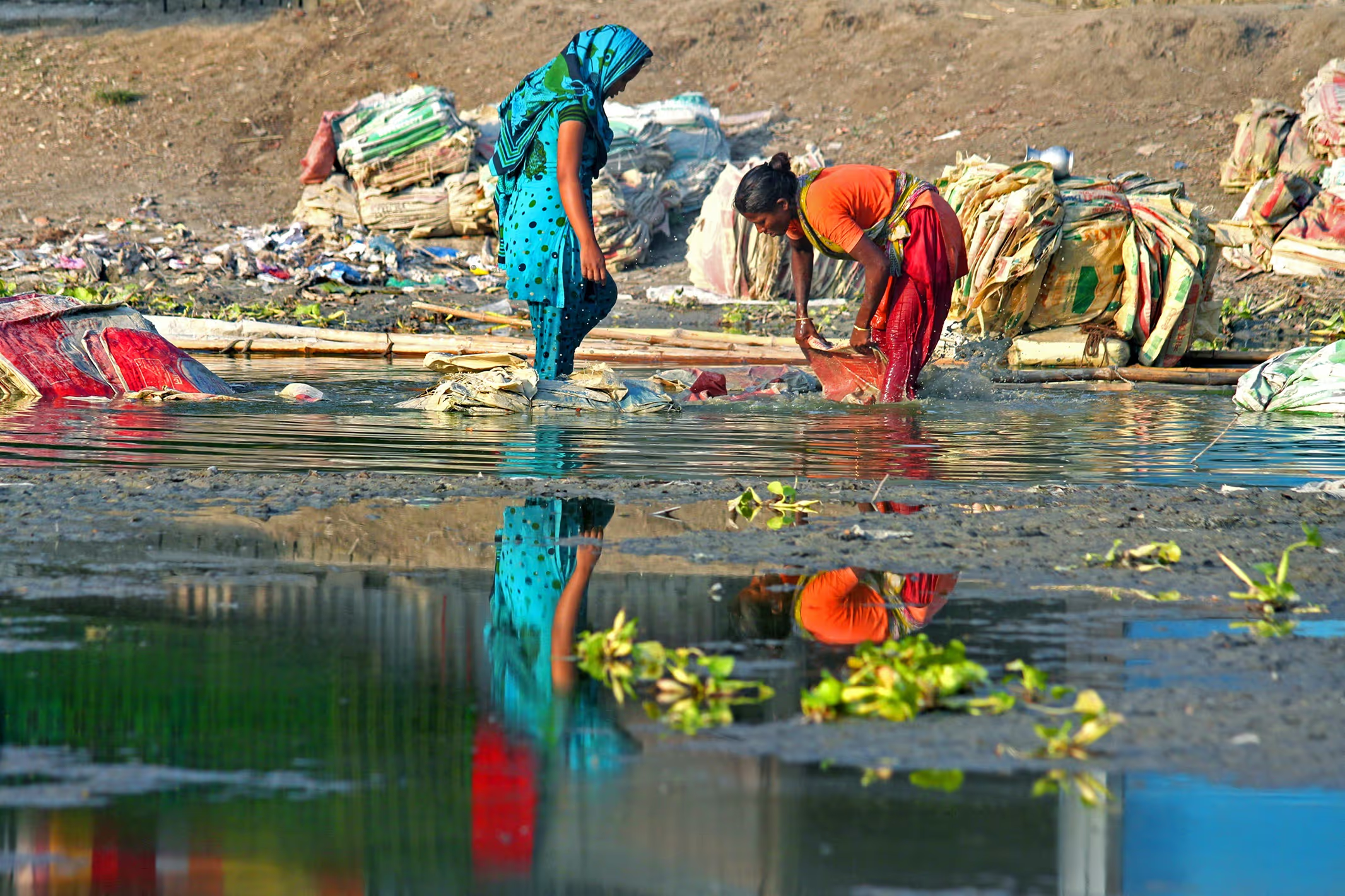
Explore Elrha
Learn more about our mission, the organisations we support, and the resources we provide to drive research and innovation in humanitarian response.